Automated QSFP Processing
.
Revolutionizing 100G/200G/400G Transceiver Manufacturing with Automated Precision
Our advanced robot automated system is specifically engineered to optimize the production of high-performance transceivers, including 100G, 200G, and 400G modules. This innovative system integrates cutting-edge features that streamline processes, ensure product quality, and reduce downtime, ultimately improving efficiency in high-volume manufacturing environments.
Key Features
-
Form Factor Compatibility: QSFP-DD
- The system supports the most widely used form factor for high-speed transceivers, ensuring seamless integration with industry standards.
- Optical Interface: LC / SC / MT-MPO
- Versatile support for different optical interfaces, including LC, SC, and MT-MPO, allowing flexibility in transceiver production across a variety of network applications.
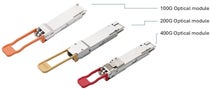
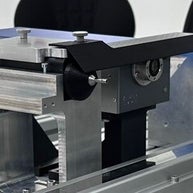
-
Auto CVI (Cleaning and Visual Inspection of Optical Interfaces)
- Automatic cleaning and high-precision visual inspection (CVI) of optical interfaces, ensuring that every transceiver meets the stringent standards required for optimal signal integrity and performance.
- Automated cleaning of optical interfaces
- Automated reporting
-
Auto Quality Control 4 X DUT
-
Comprehensive quality checks, including:
- EEPROM/Firmware Integrity Testing: Ensures the transceiver's programmable memory is correctly loaded and functioning.
- Label Conformity Check: Verifies correct labeling for compliance and traceability.
- DDM Diagnostics: Performs real-time Digital Diagnostic Monitoring (DDM) to assess parameters like temperature, voltage, and power output.
-
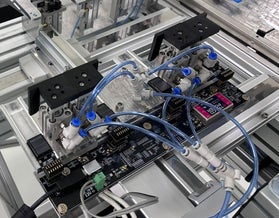
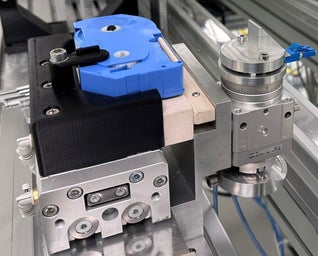
-
Optical Loopback Sensitivity Testing
- The system performs average sensitivity testing on the transmitter DUT (TxDUT) while the receiver DUT (RxDUT) is calibrated, ensuring accurate performance metrics for high-speed signal transmission.
- Connector cleaning every test.
- Cleaning media consumption monitoring
-
Automatic Loading/Unloading 250 Transceivers.
- The system can handle the automated loading and unloading of up to 25 trays, significantly enhancing throughput and reducing manual intervention in high-volume production environments.
- Dispensing process trays as devices are consumed and stacking checked devices
- Isolating triage devices of non conformance.
- Database of device test results.
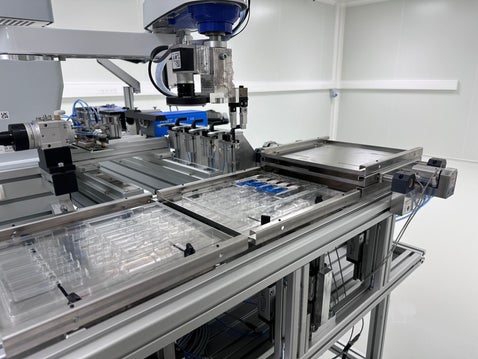
Why This System is Essential for 100G, 200G, and 400G Transceiver Manufacturing
-
Increased Production Efficiency
- Automation reduces the need for manual handling and inspection, accelerating production cycles and ensuring a consistent flow of transceivers without bottlenecks.
-
Improved Quality Assurance
- The integration of automatic cleaning, visual inspection, and electrical testing guarantees that every transceiver produced meets industry standards for performance and reliability, reducing failures and returns.
-
Versatile Compatibility
- Supporting multiple optical interfaces and form factors, this system can be adapted for a range of transceiver designs, making it an ideal solution for manufacturers focused on producing 100G, 200G, and 400G modules.
-
Cost Savings
- By automating key processes such as CVI, EEPROM testing, and sensitivity calibration, labor costs are minimized, and production accuracy is maximized, leading to long-term cost savings for manufacturers.
-
Scalability
- With the ability to handle high-volume production, the system is scalable to meet growing market demands for transceivers, whether in data centers or telecom infrastructures.